Electrostatic Precipitator Applications: Working Principles, Key Industries & Limitations
What is an Electrostatic Precipitator?
An electrostatic precipitator (ESP) is an air purification device that removes fine particulate matter, such as dust, smoke, and aerosols, from industrial and commercial exhaust streams using electrostatic forces. Functioning through a two-stage process—ionization and collection—the ESP charges particles via high-voltage electrodes (corona discharge), then attracts them to oppositely charged collector plates or tubes for removal. According to the U.S. Environmental Protection Agency (EPA), ESPs achieve over 99% efficiency in capturing submicron particles, making them critical for industries like coal-fired power plants, cement manufacturing, kitchen exhaust smoke filtration, food processing and metal processing to meet regulatory standards.
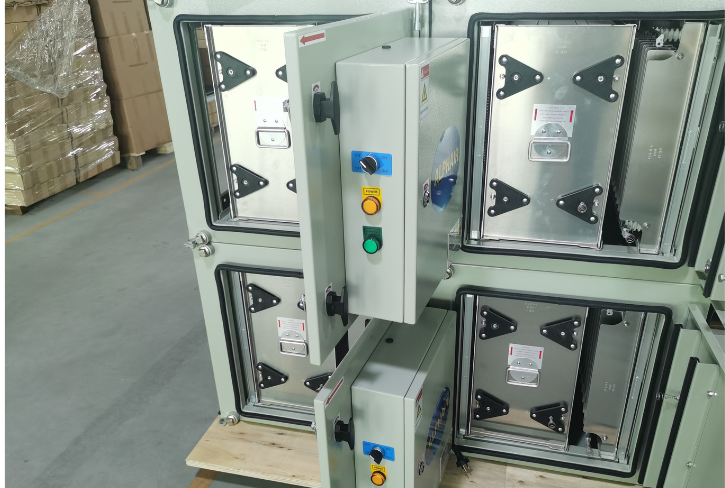
Table of Contents
What is the working principle of an Electrostatic Precipitator?
When polluted air, such as smoke or fumes, enters the ESP, it first passes through the ionization section, where a high-intensity electrical field imparts a charge to airborne particles. These particles, ranging in size from 0.01 to 10 microns, become either positively or negatively charged, depending on the system’s polarity.
Next, the charged particles move into the collection section, which consists of a series of parallel plates with alternating charges. Particles are repelled by plates of the same charge and attracted to oppositely charged plates, where they adhere and accumulate over time. In applications involving liquid pollutants, such as oil mist from cooking fumes, the collected substances gradually drain down to a collection tray at the bottom, preventing re-entrainment into the airstream.
Once the particles are removed, the purified air exits the ESP, significantly reducing airborne contaminants and improving air quality.
Note: While this explanation focuses on the plate-and-wire ESP design, it is important to note that all ESPs operate on the same fundamental principle—charging and capturing particles using electrostatic forces. The variations between different ESP types lie in their structural configurations rather than their core working mechanism.
Key Components and Their Functions
- Ionizer or Ionization Section (Charging Electrodes): The ionizer is responsible for imparting an electrical charge to pollutant particles. It consists of a series of thin discharge electrodes (wires, needles, or blades) placed between grounded plates or tubes. When a high-voltage DC field is applied, the electric field around these electrodes becomes intense enough to ionize the surrounding gas molecules, creating a corona discharge.
- Collector or Collection Plates: After being charged, particles enter the collector section, where they move towards parallel collection plates due to electrostatic attraction. The plates are arranged in alternating polarity—one set positively charged and the other grounded—to ensure efficient capture.
- High-Voltage Power Supply: The HVPS unit converts standard AC power into high-voltage DC to energize the ionizer and collection plates. A properly designed power supply ensures stable operation and efficient particle charging and collection. Equipped with overload protection, short-circuit protection, arc suppression, and automatic shutdown features, it enhances safety, reliability, and system longevity.
- Insulators: Insulators play a crucial role in maintaining electrical separation between high-voltage components and grounded parts. Since ESPs operate at high voltages, insulating materials must be highly resistant to electrical leakage and contamination.
- Auto Washing System: Keeps the collection plates clean for table filtration efficiency and low fire risk.
Physics Behind ESP Efficiency
- Coulomb’s Law & Electrostatic Attraction: The collection process in an electrostatic precipitator (ESP) is governed by Coulomb’s Law, which states that the electrostatic force between charged particles is inversely proportional to the square of the distance between them. This principle dictates how charged pollutant particles are strongly attracted to oppositely charged collection plates while being repelled by similarly charged plates, ensuring efficient separation from the air stream. The strength of this force determines how effectively particles are captured and retained.
- Migration Velocity: The speed at which charged particles travel toward the collection plates is known as migration velocity (ω) and is a crucial factor in ESP performance. This velocity is influenced by several factors, including the particle’s electrical charge (q), mass (m), air viscosity (η), and drag force exerted by the airflow. Higher charge levels and lower mass result in faster migration, while increased air resistance slows particle movement. The theoretical migration velocity can be estimated using Deutsch’s equation, which helps predict ESP collection efficiency under different operational conditions.
- Corona Discharge & Ionization Mechanisms: The corona discharge process is responsible for charging pollutant particles in an ESP. When a high voltage is applied to the ionizer wires, the surrounding air undergoes dielectric breakdown, creating a plasma of free electrons and ions. These charged species then collide with incoming pollutant particles, imparting a net charge to them. The efficiency of ionization depends on factors such as electrode geometry, applied voltage, and gas composition, all of which influence the overall charging effectiveness and particle collection efficiency.
- Secondary Electron Emission: When high-energy electrons strike a surface, they can cause the ejection of additional electrons in a phenomenon known as secondary electron emission. In an ESP, this process helps sustain the ionization mechanism by generating more free electrons that contribute to particle charging. This effect is particularly significant in high-voltage environments, where enhanced charge transfer leads to improved capture efficiency. The choice of electrode material and surface treatment can further optimize this phenomenon to maximize ESP performance.
The Top 20 Must-Know Applications of Electrostatic Precipitators (ESP) for Air Pollution Control
Commercial & Hospitality Industry
- 1. Commercial Kitchens – Removal of cooking fumes, grease, odors, and smoke in restaurants, hotels, and food courts.
- 2. Barbecue & Grilling – Purification of heavy smoke and grease emissions from BBQ and grilling operations.
Metal and Automotive Manufacturing
- 3. Metalworking & Machining – Removal of coolant mist, welding fumes, and fine metal particulates from cutting, grinding, and machining operations.
- 4. Automotive Manufacturing – Purification of exhaust, paint overspray, welding fumes, and particulate matter from automotive production.
- 5. Aerospace Industry – Treatment of emissions and fine particulates generated during precision manufacturing and coating processes.
Industrial Air Pollution Control
- 6. Chemical & Pharmaceutical Industry – Removal of harmful gases and fine particulates from chemical processing and pharmaceutical manufacturing.
- 7. Cement & Glass Manufacturing – Treatment of dust, fine particulates, and gaseous pollutants from cement kilns and glass furnaces.
- 8. Power Plants – Control of fly ash and fine particulates from coal-fired and biomass power generation.
- 9. Waste Incineration – Control of fine particulate emissions and toxic gases from waste-to-energy plants.
- 10. Textile Manufacturing – Treatment of exhaust gases from stenter machines, dyeing processes, and finishing operations.
- 11. PVC Processing & Synthetic Leather Production – Treatment of exhaust gases from PVC foaming ovens, PVC flooring, synthetic leather, and PVC gloves manufacturing.
- 12. Biomass Processing & Combustion – Removal of fine particulates, tar, and ash from biomass boilers and gasification plants.
Electronics & High-Tech Manufacturing
- 13. Electronics Manufacturing – Removal of fine particulates, smoke, and chemical vapors from semiconductor fabrication and PCB production.
Medical & Research Facilities
- 14. Healthcare & Laboratories – Removal of airborne viruses, bacteria, chemical fumes, and odors in hospitals, cleanrooms, and research labs.
Stone and Wood Processing
- 15. Stone Cutting & Processing – Capture of stone dust and fine particulate emissions generated during stone slab cutting, polishing, and grinding.
- 16. Wood Processing – Removal of sawdust, resins, and fine particulates from woodworking and panel manufacturing.
Temple Incense & Joss Paper Burning
- 17. Temple Incense & Paper Burning – Control of smoke, fine ash, and particulates generated from incense burning and paper offerings in temples.
Food Processing
- 18. Food Processing – Purification of fumes, odors, and particulate matter from frying, roasting, and drying processes.
- 19. Coffee Roasting – Capture of fine particulates, smoke, and volatile organic compounds (VOCs) generated during the roasting process.
- 20. Marine Industry – Treatment of exhaust emissions from ship engines and industrial onboard processes.
Important Note:
Electrostatic Precipitators (ESP) can be applied across the industries listed above, but it is important to note that not all exhaust gases can be directly filtered with ESP technology. Several factors must be considered before implementation, including gas temperature, humidity levels, the nature of the pollutants (solid particulates or liquid aerosols), and whether the contaminants are highly adhesive or reactive. In many cases, pre-treatment systems such as cooling, moisture control, or particulate separation may be required to ensure optimal performance and longevity of the ESP unit.
Contact Our Experts for a Tailored Air Filtration Solution
Industries Where ESP Not Be Suitable
While Electrostatic Precipitators (ESP) are highly effective for many applications, there are certain industries and exhaust conditions where ESP technology may not be the ideal solution.
- Explosive or Highly Flammable Environments – ESPs generate high-voltage electric fields, which can pose ignition risks in environments with flammable dust, gases, or vapors. Examples: Powder coating, flour milling, and oil refineries.
- Sub-Micron Gaseous Pollutants – ESPs primarily target particulate matter and may not effectively capture gaseous pollutants, volatile organic compounds (VOCs), or acidic fumes without additional treatment. Examples: Chemical manufacturing, fuel combustion emissions, and ammonia-based exhaust streams.